Fluid level sending units help detect the liquid level within a tank or container. They are an essential component of fluid detection systems used in industrial and commercial applications. While there are several different types of these sending units, they all have a similar purpose. They help the end-user of vehicles and other machinery determine fluid level at all times.
For example, a fuel level sending unit helps determine when the fuel level is getting low. A float that acts like a bobber sits directly on top of the fuel. As the fuel level in the tank adjusts, so does the float. As the float moves up and down, magnets inside of it activate reed switches in a circuit board. This is also what moves the needle on your fuel gauge.
Fluid level sending units are used across a variety of applications. Typically, fluid sending units acquired from a reputable manufacturer are reliable components. However, issues may arise if or when the sending unit fails. With proper maintenance and care, fuel sending units can last as long as the life of a vehicle, boat, or other type of machinery.
Let’s examine the reasons why sending units fail and what you can do about it.
Reasons Why Fluid Sending Units Fail
As we already noted, fluid level sending units tend to be reliable components. That’s why it’s all the more frustrating when they fail. We always recommend buying your component from an experienced manufacturer of liquid level sending units and their components. This will help you avoid failure due to a faulty part that needs replacing. Here are some other common reasons failure occurs.
Lack of Maintenance
There are several reasons why a fluid level sending unit can fail. The foremost reason is a lack of proper maintenance. For example, a dirty liquid tank can cause the float to get stuck as debris can get caught between the float and the level tube and prevent freedom of movement.
Incorrect Application
Even though all fluid sending units perform a similar function, they are not interchangeable. Manufacturers make different types of sending units out of different materials, which may not suit the environment they operate in. If you are using the incorrect sending unit , it will likely fail faster than usual, as it will be unable to keep up with the stress the equipment is placing on it.
Additional Reasons for Fluid Sending Unit Failure
While lack of maintenance and incorrect application are usually the main causes of fluid sending unit failure, there are still many other reasons these units can fail.
Here are some additional reasons for sending unit failure we have seen.
- Excessive voltage and/or voltage spike — Sending electricity that is above the unit’s power rating can burn out resistors.
- Poor installation — Installing a fluid level sending unit incorrectly could drastically shorten its lifespan, and cause a leak. Always consult the installation manual during setup.
- Incompatible fuel additives — Fuel additives may cause the float within the unit to not float properly, leading to incorrect readings.
- Impact — Physical damage, such as dropping the fluid level sending unit, could cause reed switch damage. This can ultimately cause the unit to stop working.
- Improper wiring connection — Failing to connect the unit properly to wiring could lead to it receiving inadequate power to function properly, damaging the unit’s health. In addition, poorly done wiring, such as wiring that allows water to come in contact with bare wire, can also damage the unit’s long-term usability.
- Incorrect sending unit size — All sending units have different size requirements depending on the size of tank. While having an incorrectly sized sending unit may not cause outright failure, the liquid level readings may not be accurate.
- Tampering — Only trained and approved professionals should disassemble and rework sending units. with the appropriate installation guide should handle the maintenance of fluid level sending units. A less experienced individual may damage the unit without realizing it.
- Lightning — Lightning can cause the resistors within the unit to burn out, leading to unit failure.
- Dirty Tank — Dirt, dust, and other particles can get trapped within the float, impeding its motion and leading to inaccurate liquid level readings.
Once again, in the event of fluid level sending unit failure, it’s best to contact an expert for assistance.
How to Prevent Fluid Sending Unit Failure
You can often prevent fluid level sending unit failure by closely following the instruction manual’s guidance for any tank-specific maintenance and care.
Inside the manual, there should be sections covering maintenance, including how to safely remove and replace failed fluid level sending units, as well as how often a particular unit should require maintenance. Ensure that wiring is done correctly, and that the power supply is stable and generating the right amount of power for the equipment to function properly.
Furthermore, it’s imperative to research the equipment you are using the fluid level sending unit in, and consider the type of environment the unit will reside in. Lastly, make sure you handle liquid senders with care, as accidental damage such as dropping the unit can be a cause for unit failure.
There are many fluid level sending units to choose from, and they’re all created to do specific tasks tied to measuring liquid levels in a tank or storage container. If you are ever in doubt about what unit you need, make sure to consult an expert. Using the wrong fluid sender for the job can result in immediate failure, leading to incorrect or non-existent readings about liquid level.
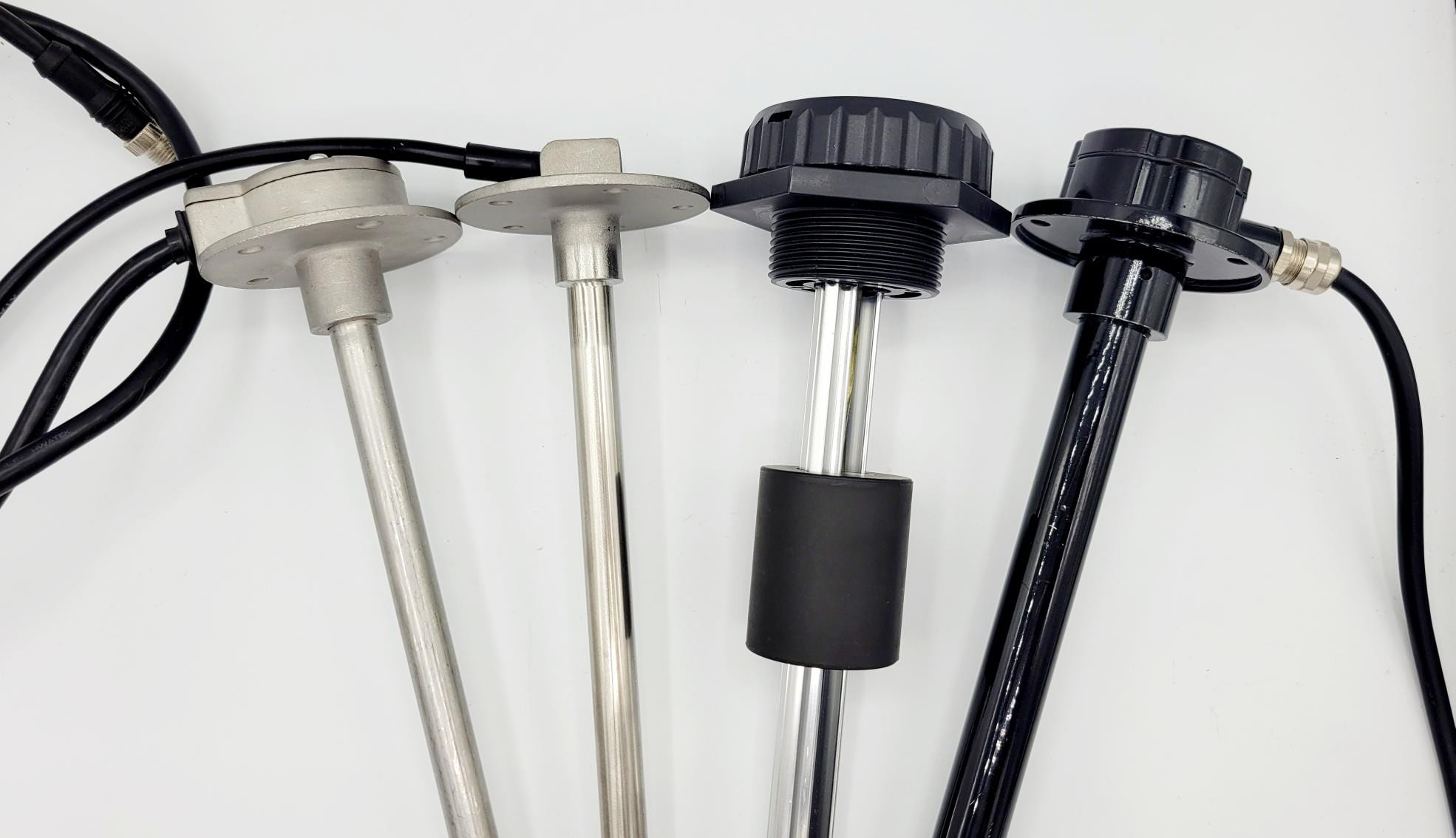
Let KUS Be Your Fluid Level Sending Unit Provider
KUS has many different types of fluid level sending units for all kinds of vehicles, marine vessels, and equipment. Our quality control measures ensure the successful operation of vehicles and equipment that utilize fluid level sending units. If you are unsure which product will best suit your needs or want to learn more about our manufacturing process, contact us. KUS has years of experience making recommendations, as it has done so for many of the world’s leading OEMs.